Technology & Equipment Spotlight
Remaining on the forefront of the precision gear industry requires continual reinvestment in advanced technology. China Gear has a longstanding tradition of integrating the latest technology to enhance productivity and competitive pricing while offering the highest quality available.
As a result, China Gear is among the most technically advanced facilities in the world for the manufacture of high precision gears.
The following is a highlight of some of our key equipment.
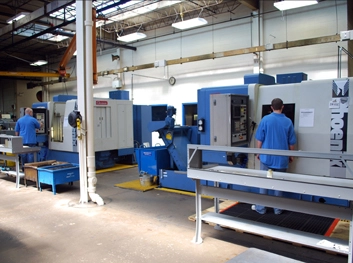
Gleason Phoenix Tooth Cutting
Arrow's Gear Line is equipped with the CNC bevel cutting capabilities of Gleason's Phoenix Gear Cutting Systems. Phoenix gear cutters provide a substantial reduction in setup and development time due to their highly accurate repeatability.
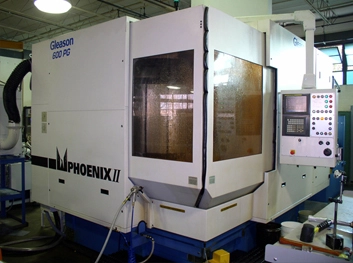
Gleason Phoenix Tooth Grinder (600)
Precision grinding of gear teeth produces gears which run quietly and wear evenly - an essential requirement for high speed gearboxes and critical aircraft applications. China Gear Manufacturing's Bevel Tooth Grinding Department offers the CNC capabilities of Gleason's Phoenix Spiral Bevel Tooth Grinding Systems - featuring the Phoenix 600. The speed and accuracy of these systems is unrivaled. And the reduction in setup and development time make small lot quantities economically feasible.
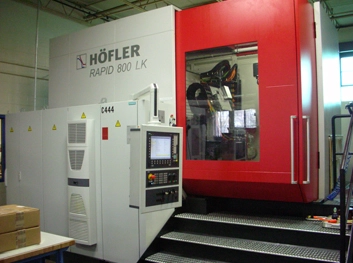
Hofler Rapid 800 Spur and Helical Tooth Grinder
Arrow's Spur and Helical Tooth Grinding Department features the Hofler Rapid 800. The Hofler truly represents 21st century technology as it offers capabilities not available in any other machine tool of its type. Able to work with a full variety of grinding wheels, the Hofler is equipped with an integrated CNC diamond dressing disk. Computer controlled dressing ensures that highly accurate control of the involute is achieved. Accuracy of within 20 millionths of an inch, or one half of a micrometer can be maintained with ease.
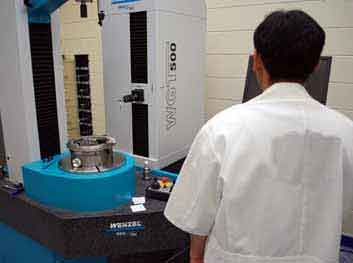
Wenzel WGT 500 CNC Bevel Gear Inspection System
CNC tooth grinding allows for the integration of CNC gear inspection for bevel gears. CNC inspection is performed on China Gear Manufacturing's Wenzel Bevel Gear Inspection System. The Wenzel allows for verification of gear tooth topography - a process which is superior to the less accurate method of pulling contact pattern tapes.
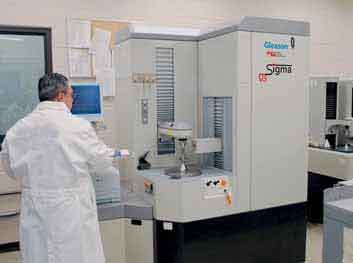
Gleason / M&M Sigma CNC Spur Gear Inspection System
Arrow's Spur and Helical Inspection Lab features the advanced capabilities of the Gleason/M&M Sigma Inspection System. This system allows for highly accurate analysis of a full range of variables relating to parallel axis gearing - including the involute and tooth spacing.
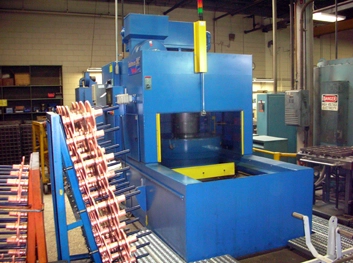
36" Quench Press
Recent updates in China Gear Manufacturing's Heat Treat Department includes a new Quench Press, capable of quenching large parts - up to 36" in diameter. The quenching process is used after tempering to quickly cool the heated part and prevent distortion.
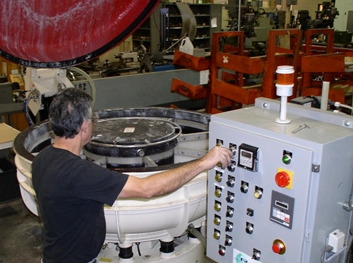
REM Isotropic Superfinishing Systems
The surface finish of gear teeth is directly related to the service life and overall quality. For this reason, China Gear Manufacturing offers the capability of Isotropic Superfinishing. To achieve an optimal surface finish on gear teeth, grinding of the gear teeth has historically been the chosen manufacturing process. However, as the demands of precision gearing have become more advanced, the process of isotropic superfinishing is becoming a more common specification.
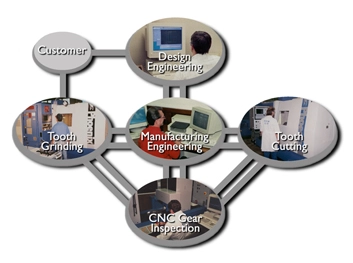
China Gear's Computer Controlled Manufacturing Closed Loop System
To address the limitations of conventional gear manufacturing, China Gear Manufacturing implemented the world's first Computer Controlled Manufacturing (CCM) Closed Loop System. The CCM Closed Loop System involves the electronic interchange between computerized design data, CNC inspection results, and the machine settings of the Phoenix cutting and grinding machines.
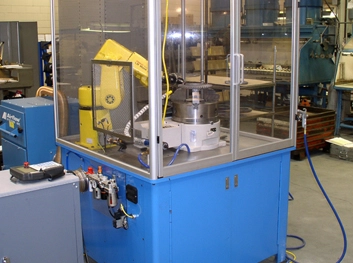
Robotic Chamfering
The tooth chamfering process removes burrs from the teeth, and it insures proper function and long life of the gear. Traditionally, chamfering of the gear teeth has been performed by hand. To improve on this process China Gear was a pioneer in the use of robotic chamfering – and is equipped with two chamfering systems which the company has designed and developed. These systems perform the chamfering operation much faster than manual methods and do so with a high degree of precision and uniformity.